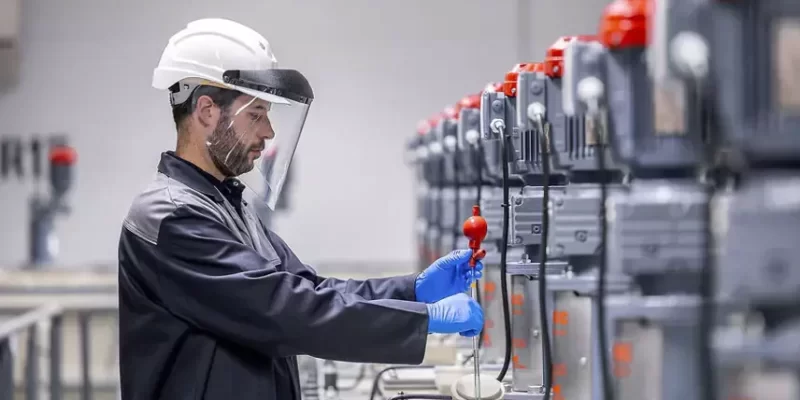
Mercedes-Benz has opened Europe’s first battery recycling plant with an integrated mechanical-hydrometallurgical process, marking a global milestone as the first automaker to establish a closed-loop battery recycling facility.
Located in Kuppenheim, Germany, this innovative plant reflects Mercedes-Benz’s commitment to sustainability and resource conservation by creating a circular economy for battery production.
Unlike traditional methods, this advanced facility is expected to achieve a recycling rate of over 96%, recovering critical materials like lithium, nickel, and cobalt, which can be repurposed for new batteries in future all-electric Mercedes-Benz vehicles.
The company has invested tens of millions of euros into this facility, supporting sustainable value creation in Germany.
Federal Chancellor Olaf Scholz and Baden-Württemberg’s Environment Minister Thekla Walker joined the opening ceremony in Kuppenheim, underscoring the project’s significance for Germany’s clean technology and automotive sectors.
Chancellor Scholz noted, “The future of the automobile is electric, and batteries are essential. Recycling is key to producing batteries sustainably.
This circular economy initiative supports our climate goals and advances Germany as a leader in cutting-edge technologies.”
Partnering with Primobius—a joint venture between SMS Group and Neometals—Mercedes-Benz has received additional funding from Germany’s Federal Ministry for Economic Affairs and Climate Action.
This scientific research collaboration involves three German universities to optimize the recycling process, logistics, and reintegration of recycled materials, contributing to future scaling of battery recycling capabilities across the country.
The plant integrates every step of the recycling process, from shredding battery modules to drying and refining active battery materials.
In its mechanical process, it separates materials like plastics, copper, aluminum, and iron, while the hydrometallurgical stage isolates “black mass,” or electrode-active materials, and extracts valuable metals in a multi-step chemical process. The recyclates meet battery-grade quality standards, making them viable for new battery cells.
This hydrometallurgical process offers advantages over traditional pyrometallurgy, as it consumes less energy and produces less waste.
Operating at lower temperatures of up to 80 degrees Celsius, it is more energy-efficient, and the plant’s operations are net carbon-neutral, powered entirely by green energy.
The facility’s 6,800-square-meter rooftop includes photovoltaic panels with over 350 kW peak capacity, supporting Mercedes-Benz’s commitment to sustainable manufacturing.
With an annual recycling capacity of 2,500 tonnes, the Kuppenheim plant is equipped to provide materials for over 50,000 new battery modules for all-electric Mercedes-Benz models. The expertise gained from this facility is expected to support larger-scale production in the future.
This facility is a key part of Mercedes-Benz’s “Design for Circularity” approach, which emphasizes circular design, value retention, and closing the material loop.
The company’s holistic approach to circular battery systems is integrated from the initial design phase through to production, including at its new eCampus in Stuttgart-Untertürkheim, which opened in 2024 to advance battery cell development.
By ensuring net carbon-neutral production in its battery factories across three continents, Mercedes-Benz is positioning itself at the forefront of sustainable, locally produced electric mobility solutions.