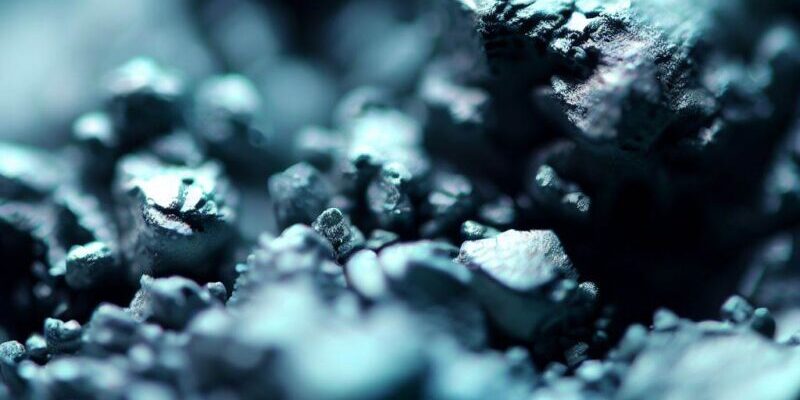
In the 1980s, rechargeable lithium metal batteries that used liquid electrolytes were considered the next big thing, penetrating the market in early portable phones.
But they had a propensity to combust when charged. The lithium atoms that shuttle between the electrodes tended to build tree-like filaments called dendrites on the electrode surfaces, eventually shorting the battery and igniting the flammable electrolyte.
The lithium ion battery — a more stable but less energy-dense technology — was introduced in 1991 and quickly became the new standard.
These batteries replaced lithium metal with graphite anodes that absorb the lithium and prevent dendrites from forming but also come with performance costs.
Current lithium ion batteries max out with a total energy density around 600 watt-hours per liter (Wh/L) at the cell level. In principal, solid-state batteries can reach 1,200 Wh/L.
By using a ceramic, solid-state electrolyte, engineers can harness the power of lithium metal batteries without the historic issues of poor durability and short-circuiting.
A rechargeable battery technology was developed that could double the output of today’s lithium ion cells — drastically extending electric vehicle ranges and time between cellphone charges — without taking up any added space.
To solve lithium metal’s combustion problem, a ceramic layer was created that stabilizes the surface, keeping dendrites from forming and preventing fires.
It allows batteries to harness the benefits of lithium metal — energy density and high conductivity — without the dangers of fire or degradation over time.
In earlier solid-state electrolyte tests, lithium metal grew through the ceramic electrolyte at low charging rates, causing a short circuit like that in liquid cells.
The problem was solved with chemical and mechanical treatments that provide a pristine surface for lithium to plate evenly, effectively suppressing the formation of dendrites or filaments. Not only does this improve safety, it enables a dramatic improvement in charging rates.
Until now, the rates at which lithium could be plated would mean a lithium metal car battery would need to charge more than 20 to 50 hours to get to full power. The new battery can be charged in three hours or less.
In testing the ceramic electrolyte, no visible degradation is observed after long-term cycling. Bulk solid-state electrolytes enable cells that are a drop-in replacement for current lithium ion batteries and could leverage existing battery manufacturing technology.