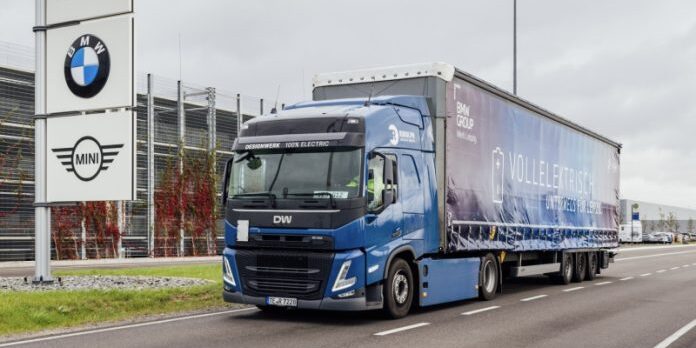
BMW Group is accelerating the shift to electric logistics with two fully electric trucks now transporting components between the logistics center and high-voltage battery production halls at its Leipzig plant.
These trucks, manufactured by DesignWerk, will collectively save an estimated nine tonnes of CO₂ emissions annually compared to diesel-powered trucks.
The trucks travel an eight-kilometer round trip up to 12 times daily, transporting essential parts such as battery cells and modules for e-drive production.
Operating around the clock in three shifts, these vehicles connect the logistics warehouse on BMW Allee with the high-voltage battery assembly halls.
Each truck displays a battery symbol, signifying its emissions-free role in Leipzig’s electric production network.
Since 2021, BMW Group Plant Leipzig has been producing e-components, and as of early 2024, it manages the full production process of high-voltage batteries for the fifth generation.
The plant’s facilities include five cell coating lines, three module production lines, and two assembly lines, supporting models like the MINI Countryman Electric, BMW iX1, iX2, i4, i5, and iX.
The facility, occupying over 150,000 m², has a team of about 1,000 employees dedicated to producing up to 300,000 high-voltage batteries annually. BMW has invested over €900 million in e-component production at this plant.
Powered by lithium iron phosphate (LFP) battery systems, each DesignWerk truck boasts four electric motors—delivering a total of 610 hp—and is based on Volvo truck models.
These electric trucks are three times more energy-efficient than diesel equivalents and are recharged during driver breaks, taking around 1.5 hours to reach an 80% charge on their 340 kWh batteries, which can be charged up to 3,000 times.
This initiative represents BMW’s commitment to sustainable logistics and localized, emissions-free transport as part of its broader push for electrification across its production network.